AKADEMIA LEAN
Powstała z myślą o Twoich potrzebach
CZYM JEST AKADEMIA LEAN?
Stwórz z nami nowy model pracy, dzięki któremu pracownicy ograniczą marnotrawstwo i mądrze zaczną doskonalić swoje umiejętności, a kadra zarządzająca zapewni szybki przepływ, skuteczność oraz efektywność procesów.
Pamiętaj: warunkiem koniecznym do odniesienia sukcesu, pracując zgodnie z wartościami lean jest zaangażowanie.
W Akademii Lean Management nauczysz się podejścia do zarządzania opartego na elastyczności, wysokiej jakości, zwiększaniu wydajności, eliminowaniu marnotrawstwa i ciągłym doskonaleniu. Poznasz narzędzia, których prawidłowe stosowane poprowadzą Twój zespół do najlepszych dla Was rozwiązań.
UDZIAŁ W AKADEMII LEAN POMOŻE CI:
CZEGO UCZYMY W AKADEMII LEAN?
Zanim rozpoczniemy Akademię Lean, przeprowadzimy profesjonalną diagnozę potrzeb Twojej organizacji. Wyniki diagnozy pomogą Ci zdecydować, które spośród poniższych tematów szkoleń są Tobie i Twoim pracownikom najbardziej potrzebne.
STANDARD SZCZUPŁEGO ZARZĄDZANIA
MODUŁ I: STANDARD SZCZUPŁEGO ZARZĄDZANIA
ZACZYNAJ Z WIZJĄ KOŃCA: Wprowadzenie do Lean Management
Początek naszej drogi to dwudniowe Wprowadzenie do Lean Management – japońskiej filozofii zarządzania opartej na wartościach, elastyczności i ograniczeniu marnotrawstwa, która stanowi dziś metodykę prowadzenia sprawnych organizacji.
Ramowy program szkolenia
- Podstawowe metody i idea ciągłego doskonalenia procesów w organizacji.
- Rozróżnienie efektywności zasobów i efektywności przepływu.
- Diagnozowanie potencjałów w organizacji i zwiększenie jej efektywności.
- Analiza dostępnych danych jako punkt wyjścia do obecnego poziomu marnotrawstwa w firmie.
- Wizualizacja jako wsparcie zarządzania. Poznanie zasad zarządzania wizualnego.
- Strategia i cele wdrożenia koncepcji Lean w przedsiębiorstwie.
- Motywowanie pracowników do podążania za zmianą.
- Skuteczne narzędzia komunikacji wewnątrz przedsiębiorstwa dla wdrożenia Lean.
- Zarządzanie zmianą.
- Jak znaleźć czas na doskonalenie?
NAPRAWIAJ – efektywne rozwiązywanie problemów i ciągłe doskonalenie.
Poznaj efektywną metodykę rozwiązywania problemów „Problem solving”. Zbuduj z nami adekwatne dla Twojego przedsiębiorstwa narzędzia konstruktywnego i systematycznego analizowania i skutecznej eliminacji problemów.
Ramowy program szkolenia:
- Wprowadzenie do koncepcji Problem Solving.
- Główne pojęcia i narzędzia związane z rozwiązywaniem problemów.
- Metody pracy w zespołach projektowych a rozwiązywanie problemów.
- Kultura nastawiona na rozwiązywanie problemów.
- Ciągłe doskonalenie procesów.
- Warsztaty praktyczne – implementacja poznanych metod, technik i narzędzi w kontekście skuteczności rozwiązywania problemów.
Ludzie w podejściu KAIZEN.
W japońskim „Kai” oznacza zmiany, a „Zen” – na lepsze. W procesach biznesowych odnosi się do ciągłego doskonalenia poprzez stopniową eliminację wykrytych niezgodności i budowę struktury odpowiedzialności. Program Kaizen spośród innych metod Lean wyróżnia się tym, że angażuje w proces doskonalenia wszystkich pracowników zaangażowanych w działanie procesu.
Ramowy program szkolenia:
- Geneza i kluczowe zagadnienia programu Kaizen.
- Metody angażowania pracowników w rozwój procesów.
- 7 kroków KAIZEN w procesie rozwiązywania problemów.
- Budowanie efektywnego programu sugestii pracowniczych – praca nad case firmy.
- System zgłaszania pomysłów usprawnień.
- Wdrażanie KAIZEN w przedsiębiorstwie: struktura odpowiedzialności i organizacja zespołów KAIZEN.
- Rozwiązania możliwe do zastosowania przy wdrożeniu programu Kaizen.
MODUŁ II: ZESPÓŁ PRACOWNIKÓW W KULTURZE LEAN
NAJPIERW RZECZY NAJWAŻNIEJSZE: 5S organizacja wydajnego miejsca pracy.
Poznaj metodykę organizowania wydajnego miejsca pracy według pięciu japońskich zasad mających na celu właściwą organizację środowiska pracy, doskonalenie kultury organizacyjnej przedsiębiorstwa oraz zwiększenie stabilności procesów.
5S TO:
- Sortowanie (jap. Seiri).
- Systematyka (jap. Seiton).
- Sprzątanie (jap. Seiso).
- Standaryzacja (jap. Seiketsu).
- Samodyscyplina (jap. Shitsuke).
5S to kluczowa technika Lean Management, wdrażana jako jedna z pierwszych, stanowiąca podstawę do dalszych działań optymalizujących procesy w firmach produkcyjnych i usługowych.
Ramowy program szkolenia
- Motywy wdrażania 5S.
- Elementy składowe 5S.
- Przygotowanie do wdrożenia – audyt środowiska pracy.
- Standaryzacja w miejscu pracy.
- Wizualizacja jako wsparcie zarządzania.
- Warunki skutecznego wdrożenia 5S w firmie.
- Wyzwania, jakie mogą pojawić się przy wdrażaniu.
- Korzyści wynikające z dobrze wdrożonego 5S.
- Strategia wdrożenia 5S w Twojej firmie.
- Symulacja wybranego procesu i propozycja jego ulepszenia.
DBAJ – TPM i poprawa efektywności parku maszynowego.
Dbając o maszyny, dbasz o bezpieczeństwo i komfort pracy Twoich pracowników. Szkolenie rekomendowane dla osób z działów: utrzymania ruchu, produkcji, planowania produkcji. Warsztaty rozwiążą problem braku stabilizacji w procesach produkcyjnych.
Ramowy program szkolenia
- Straty zmniejszające dostępność maszyn. Cele TPM.
- Podstawowe wskaźniki stosowane w podejściu TPM.
- Narzędzia stosowane w TPM.
- Najlepsze praktyki utrzymania sprawnego parku maszynowego.
- Strategie utrzymania ruchu – ukierunkowane doskonalenie.
- Wdrożenie TPM – plan uproszczony i organizacja TPM.
- Doskonalenie procesów w parku maszynowym.
- Koszty Utrzymania Ruchu.
Skracanie czasu przezbrojeń metodą SMED.
Celem szkolenia jest poznanie i wdrożenie zbioru narzędzi i technik metodyki SMED (Single Minute Exchange of Die), które umożliwiają skracanie czasów przezbrajania maszyn, urządzeń i procesów produkcyjnych. Akronim SMED pochodzi od angielskiego Single Minute Exchange of Die, oznaczającego wymianę formy w ciągu jednocyfrowej liczby minut. Głównym założeniem metody jest przeprowadzenie każdego przezbrojenia w jednostkowej liczbie minut (do 10 minut) poprzez taki podział i uproszczenie całego procesu, aby przezbrojenia dokonywane były z użyciem jak najmniejszej ilości narzędzi.
Ramowy program szkolenia
- Za pomocą jakich narzędzi skrócić czas przezbrojeń?
- Efektywne wykorzystanie możliwości procesu.
- Typy strat utrudniające płynne przeprowadzenie procesu przezbrojeń.
- SMED. Praktyczne zrealizowanie pełnego cyklu metody SMED – trening zastosowania metody.
ZESPÓŁ PRACOWNIKÓW W KULTURZE LEAN
KOMU DEDYKUJEMY AKADEMIĘ LEAN?
Dla osób zarządzających
Dla kadry
Dla pracowników, których zadania zawodowe i miejsca pracy mają zostać usprawnione dzięki wdrożeniu zasad Lean Menagement
CZY SIĘ NA TYM ZNAMY?
SIŁĄ AKADEMII SĄ NASI TRENERZY
Od 2008 roku budujemy silny i skuteczny team ekspertów. Wiemy jak ważne są procesy rozwojowe, które nam powierzacie. Z tego powodu każdy nasz trener jest częścią zespołu SENSE. Mamy wspólne wartości, standardy, razem pracujemy nad lepszymi usługami. Budujemy z Wami relacje i dbamy o wizerunek projektów. Jesteśmy po to, by skutecznie pomagać Wam w rozwoju.
METODYCZNIE I ELASTYCZNIE ZARZĄDZAMY PROJEKTAMI
GDZIE WDRAŻAMY LEAN MANAGEMENT?
Uczymy stosować zasady szczupłego zarządzania także w wybranych obszarach funkcjonalnych przedsiębiorstwa, takich jak rachunkowość (lean accounting), rozwój nowych produktów (lean product development) i BHP (lean safety).
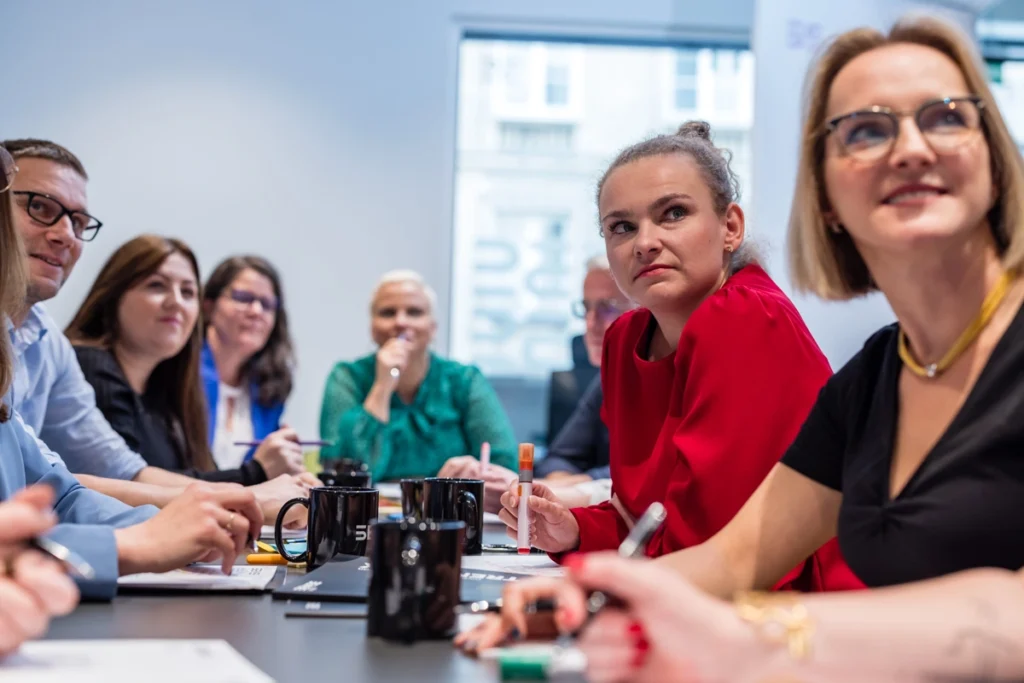
- Sektor produkcyjny (lean production)
- Sektor usługowy (lean service)
- Służba zdrowia (lean healthcare)
- Budownictwo (lean construction)
- Szkolnictwo wyższe (lean higher education)
- Instytucje sektora publicznego (lean government)
- Logistyka (lean logistics) i łańcuchach dostaw (lean supply chain)
- Sektor IT (lean IT), w szczególności produkcja oprogramowania (lean software development)
ZDOBĄDŹ DOFINANSOWANIE
Akademia Lean w pełnej wersji uszyta jest dla 12 osób. Skorzystaj z jasnego i przejrzystego modelu finansowania!
Kupując Akademię otrzymasz nasze wsparcie w aplikowaniu o 80% dofinansowanie z Europejskiego Funduszu Społecznego w cenie! Jesteśmy liderami w pozyskiwaniu środków – od 5 lat zajmujemy 1 miejsce w kraju w zakresie liczby i wartości pozyskanych dotacji.
Dofinansowania
NASI WYBRANI KLIENCI
Monika Zamojska
Kierownik Szkoleń nietechnicznych i jakości, Volkswagen Group Polska
Prof. dr hab. Ryszard Naskręcki
Prorektor Uniwersytetu im. Adama Mickiewicza w Poznaniu
Małgorzata Badowska
Specjalista ds. Personalnych, York sp. z o.o. s.k.
Dariusz Haraj
CEO / Managing Director OneDayMore
Paweł Skrzypczak
Prezes Zarządu Primavika
NASI WYBRANI KLIENCI
Monika Zamojska
Kierownik Szkoleń nietechnicznych i jakości, Volkswagen Group Polska
Prof. dr hab. Ryszard Naskręcki
Prorektor Uniwersytetu im. Adama Mickiewicza w Poznaniu
Małgorzata Badowska
Specjalista ds. Personalnych, York sp. z o.o. s.k.
Dariusz Haraj
CEO / Managing Director OneDayMore
Paweł Skrzypczak
Prezes Zarządu Primavika
SKONTAKTUJ SIĘ Z NAMI